TÓM TẮT:
Tái chế thủy tinh thành vật liệu xốp mang lại nhiều lợi ích kinh tế và môi trường. Vật liệu xốp có độ xốp cao, khả năng cách nhiệt, cách âm, chống cháy và chịu nước, được ứng dụng trong nhiều lĩnh vực. Việc tái chế thủy tinh giúp giảm thiểu ô nhiễm và tạo ra vật liệu có giá trị sử dụng cao. Quá trình tạo xốp từ thủy tinh thải phụ thuộc lớn vào các giai đoạn biến dạng của thủy tinh tại các nhiệt độ khác nhau. Nghiên cứu này tập trung vào khảo sát thay đổi tính chất của vật liệu xốp từ thủy tinh thải ở giai đoạn bắt đầu biến dạng (620oC) và giai đoạn nở phồng (830oC). Kết quả cho thấy đã tạo được vật liệu xốp bằng cách nung thủy tinh thải và phụ gia thủy tinh lỏng ở nhiệt độ biến dạng và nhiệt độ nở phồng. Nung mẫu ở nhiệt độ nở phồng tạo nên vật liệu có độ xốp cao hơn nhiệt độ biến dạng.
Từ khóa: tái chế thủy tinh, tái chế, giảm thiểu ô nhiễm, vật liệu xốp, bột thủy tinh thải.
1. Đặt vấn đề
Trong bối cảnh lượng rác thải thủy tinh gia tăng nhanh chóng tại Việt Nam, việc tái chế thủy tinh trở thành một vấn đề cấp bách. Tỷ lệ tái chế thủy tinh hiện tại của Việt Nam chỉ đạt khoảng 10%, thấp hơn đáng kể so với các quốc gia phát triển, dẫn đến phần lớn lượng thủy tinh thải bị chôn lấp. Thủy tinh, với tính chất không phân hủy, có thể tồn tại trong môi trường hàng triệu năm, gây ra những hệ lụy nghiêm trọng về ô nhiễm. Do đó, việc nghiên cứu và phát triển các phương pháp tái chế thủy tinh hiệu quả không chỉ giúp giảm thiểu lượng chất thải chôn lấp mà còn mang lại lợi ích to lớn về mặt bảo vệ môi trường, tiết kiệm tài nguyên và năng lượng. Nghiên cứu trong lĩnh vực này đóng vai trò then chốt trong việc giải quyết các thách thức môi trường hiện tại, hướng tới một tương lai phát triển bền vững cho cộng đồng.
Trong các nghiên cứu về tái chế thủy tinh thải, tạo vật liệu xốp từ thủy tinh thải đang là hướng nghiên cứu được quan tâm [1]. Một số nghiên cứu tiêu biểu theo định hướng này có thể kể đến như: Bùi Khắc Thạch và các cộng sự đã nghiên cứu việc tái chế thủy tinh thải từ tấm pin quang điện để sản xuất vật liệu xốp thủy tinh [2]; Pat Sooksaen và cộng sự đã nghiên cứu quy trình chế tạo bọt kính nhẹ với ứng dụng cách nhiệt từ chai kính thải [3]; Seun Samuel và các cộng sự đã tiến hành tổng hợp bọt thủy tinh từ kính thải và sử dụng thủy tinh lỏng làm chất tạo bọt [4]; Hesky và các cộng sự (2015) đã nghiên cứu việc sử dụng thủy tinh lỏng làm chất tạo bọt thân thiện với môi trường để sản xuất vật liệu xốp [5].
Các nghiên cứu trên cho thấy vật liệu xốp từ thủy tinh thường được sản xuất bằng phương pháp gia nhiệt, trong đó hỗn hợp bột thủy tinh và các phụ gia đặc biệt tạo xốp được nung ở nhiệt độ vượt quá ngưỡng biến mềm của thủy tinh. Thông thường các phụ gia tạo xốp thường là các hợp chất có gốc cacbon như cacbonat và SiC [6, 7]. Quá trình biến mềm của thủy tinh thúc đẩy sự kết khối của các hạt thủy tinh, tạo thành cấu trúc liên tục. Các nghiên cứu cho thấy, các giai đoạn biến dạng của phối liệu quyết định lớn đến các tính chất vật lý của vật liệu xốp từ thủy tinh thải. Trong nghiên cứu này, chúng tôi sẽ tiến hành khảo sát các tính chất vật lý của vật liệu xốp từ thủy tinh thải trong hai giai đoạn biến dạng quan trọng là bắt đầu biến dạng và nở phồng. Các tính chất vật lý như phân bố lỗ xốp, độ xốp, độ hút nước và khối lượng thể tích đã được lựa chọn để làm cơ sở đánh giá.
2. Nguyên liệu và phương pháp phân tích
2.1. Nguyên liệu
Thủy tinh thải (TTT) được lấy từ Công ty TNHH Thiên Phú - Long An. Phụ gia tạo xốp là thủy tinh lỏng (TTL). Thủy tinh lỏng (Na2O.nSiO2.mH2O) là sản phẩm thương mại có tỉ trọng 1,45 g/cm3. Thành phần hóa của thủy tinh thải và thủy tinh lỏng được xác định bằng phương pháp huỳnh quang tia X (XRF - X-ray fluorescence). Kết quả được trình bày ở Bảng 1.
Bảng 1. Thành phần của nguyên liệu (% khối lượng)
Nguyên liệu |
SiO2 |
CaO |
Na2O |
MgO |
Al2O3 |
K2O |
Fe2O3 |
PbO |
SO3 |
Khác |
MKN |
TTT |
53,49 |
9,25 |
8,05 |
2,65 |
0,96 |
0,34 |
0,17 |
0,08 |
0,08 |
0,17 |
22,47 |
TTL |
69,15 |
0,40 |
27,82 |
- |
1,66 |
- |
0,07 |
n.d |
- |
0,90 |
0,00 |
Nguồn: Nhóm tác giả thực hiện
2.2. Quá trình tạo mẫu
Thủy tinh thải sau khi nghiền và sàng qua sàng 0,63 mm được trộn với thủy tinh lỏng theo các tỷ lệ khối lượng TTT/TTL là 92/8. Ngoài ra, một lượng nước được trộn thêm vào hỗn hợp với tỉ lệ 20% theo khối lượng TTT để đảm bảo độ linh động của phối liệu cho quá trình tạo hình. Sau khi nhào trộn để đạt hỗn hợp đồng nhất, phối liệu sẽ được đổ vào khuôn có kích thước Φ42x18 mm và đem đi sấy để loại bỏ độ ẩm. Sau đó, các mẫu sẽ được nung ở các nhiệt độ biến dạng và nhiệt độ nở phồng của thủy tinh với tốc độ nâng nhiệt 3°C/phút và thời gian lưu là 4h để tạo ra lỗ xốp trong vật liệu (nhiệt độ nung xác định dựa trên kết quả từ mô phỏng kính hiển vi nhiệt). Sau quá trình nung, mẫu sẽ được tiến hành đo các tính chất cơ lý và kích thước lỗ xốp để đánh giá hiệu quả của quy trình sản xuất vật liệu xốp từ thủy tinh thải.
2.3. Phương pháp phân tích
Các phương pháp phân tích bao gồm: Huỳnh quang tia X (XRF - X-ray fluorescence) để xác định thành phần hóa của nguyên liệu; Mô phỏng kính hiển vi nhiệt (HM - Heating microscope) để xác định các nhiệt độ đặc trưng của phối liệu; Kính hiển vi kỹ thuật số để phân tích lỗ xốp; Các tính chất khác như khối lượng thể tích, độ xốp, và độ hút nước được xác định theo tiêu chuẩn ASTM C20-00.
3. Kết quả và bàn luận
3.1. Xác định các nhiệt độ đặc trưng của phối liệu
Hình 1 là kết quả phân tích kính hiển vi nhiệt của mẫu sử dụng 8% TTL. Kết quả cho thấy sự thay đổi hình dạng của mẫu chi làm 3 giai đoạn rõ rệt:
- Giai đoạn 1: Tương ứng với khoảng nhiệt độ từ 200 - 620oC. Trong khoảng nhiệt này, kích thước của mẫu gần như thay đổi rất ít, điều này cho thấy không có nhiều những biến đổi hóa lý xảy ra trong giai đoạn này.
- Giai đoạn 2: Tương ứng với khoảng nhiệt độ từ 620 - 830oC. Trong khoảng nhiệt độ này, mẫu tăng kích thước nhanh chóng. Điều này thể hiện các quá trình tạo xốp cho vật liệu chủ yếu diễn ra trong giai đoạn này.
- Giai đoạn 3: Tương ứng với nhiệt độ từ 830 - 1020oC. Trong giai đoạn này, mẫu giảm kích thước nhanh chóng. Kết quả cho thấy thủy tinh thải bắt đầu nóng chảy trong giai đoạn này và làm giảm kích thước của mẫu.
Từ kết quả phân tích cùng với sự thay đổi giá trị H/Ho (%), hệ phối liệu có những mốc nhiệt độ đặc trưng bao gồm: 620oC là nhiệt độ bắt đầu biến dạng; 838oC là nhiệt độ nở phồng; 980oC là nhiệt độ cầu; 1003oC là nhiệt độ bán cầu; và 1020oC là nhiệt độ chảy tràn. Với mục tiêu tạo vật liệu xốp thì nhiệt độ từ 620 - 830oC là nhiệt độ thích hợp để tạo mẫu. Vì vậy, 620oC và 830oC là nhiệt độ lựa chọn để khảo sát các tính chất của vật liệu xốp được tạo từ TTT và TTL.
Hình 1: Kết quả phân tích kính hiển vi nhiệt mẫu 8% TTL
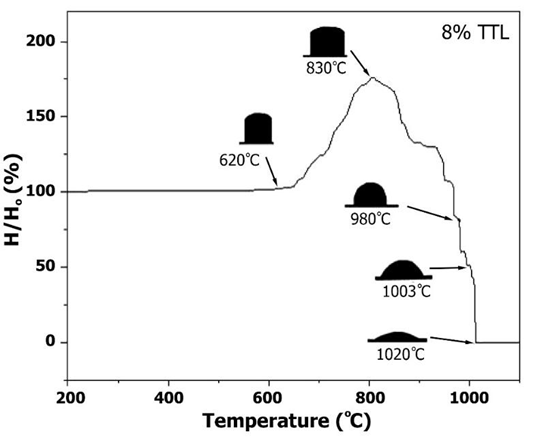
Nguồn: Nhóm tác giả thực hiện
3.2. Sự phân bố lỗ xốp
Hình 2 là kết quả phân bố lỗ xốp và tần suất xuất hiện lỗ xốp ở các mẫu nung ở 620oC và 830oC. Kết quả thu được là giá trị đếm trên bề mặt mẫu có đường kính 42 mm.
Kết quả Hình 2 cho thấy nhìn chung, cả 2 mẫu đều đã hình thành lỗ xốp và kích thước lỗ xốp phân bố từ 0 - 5,5 mm. Tuy nhiên, có sự khác biệt rõ ràng giữa mẫu nung ở nhiệt độ bắt đầu biến dạng và nhiệt độ nở phồng. Mẫu nung ở nhiệt độ nở phồng (830oC) có số lượng lỗ xốp bề mặt nhiều hơn đáng kể so với mẫu nung ở nhiệt độ biến dạng (620oC). Ngoài ra, kích thước lỗ xốp ở nhiệt độ nung 830oC cũng lớn hơn so với tập trung lớn nhất ở khoảng 1,0 - 1,5 mm so với mẫu 620oC tập trung trong khoảng 0,5 - 1 mm. Kết quả cho thấy tùy theo mục đích sử dụng lỗ xốp chúng ta có thể quyết định chọn nhiệt độ nung thích hợp để tạo vật liệu xốp từ thủy tinh thải. Với mục tiêu cần lỗ xốp bé, số lượng lỗ xốp không cần quá lớn có thể lựa chọn nhiệt độ biến dạng làm nhiệt độ nung. Ngược lại, cần độ xốp có số lượng và kích thước lớn thì nhiệt độ nở phồng có thể được lựa chọn để nung mẫu.
Hình 2: Sự phân bố lỗ xốp của mẫu nung ở 620oC và 830oC
Nguồn: Nhóm tác giả thực hiện
3.3. Độ xốp, độ hút nước và khối lượng thể tích
Hình 3: Độ xốp, độ hút nước và khối lượng thể tích các mẫu
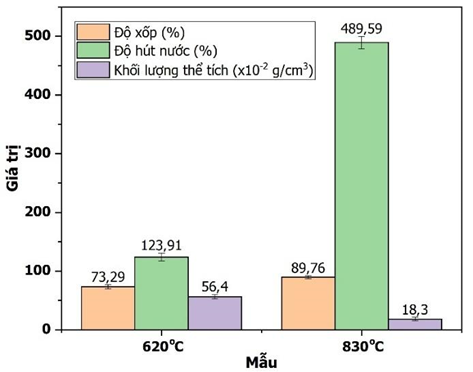
Nguồn: Nhóm tác giả thực hiện
Kết quả phân tích một số tính chất vật lý quan trọng của vật liệu xốp, bao gồm độ xốp, độ hút nước và khối lượng thể tích, được trình bày chi tiết trên Hình 3. Các dữ liệu này cung cấp chi tiết hơn các đặc tính của vật liệu, đồng thời củng cố những kết luận đã được rút ra từ Hình 2, làm nổi bật vai trò của nhiệt độ nung trong việc định hình cấu trúc và tính chất của vật liệu xốp.
Điểm đáng chú ý trong kết quả này là sự khác biệt rõ rệt về tính chất xốp giữa mẫu vật liệu nung ở nhiệt độ nở phồng (830°C) và mẫu nung ở nhiệt độ biến dạng (620°C). Mẫu vật liệu nung ở 830°C thể hiện tính chất xốp vượt trội, thể hiện qua độ xốp và độ hút nước cao hơn đáng kể so với mẫu nung ở 620°C. Cụ thể, độ xốp của mẫu nung ở 830°C đạt 89,76%, trong khi đó, ở mẫu nung 620°C, giá trị này chỉ là 73,29%. Tương tự, độ hút nước của mẫu 830°C là 489,59%, cao hơn rất nhiều so với 123,91% của mẫu 620°C.
Sự gia tăng về độ xốp này có mối liên hệ mật thiết với sự giảm khối lượng thể tích. Mẫu nung ở 830°C, với độ xốp cao, có khối lượng thể tích là 0,183 g/cm³, thấp hơn đáng kể so với mẫu nung ở 620°C, có khối lượng thể tích là 0,564 g/cm³. Điều này cho thấy rõ ràng rằng cấu trúc xốp hơn của mẫu 830°C dẫn đến khối lượng trên một đơn vị thể tích nhỏ hơn.
Cuối cùng, giá trị khối lượng thể tích thấp ở cả hai mẫu, mặc dù có sự chênh lệch nhất định, chứng minh rằng vật liệu xốp đã được tạo ra thành công từ hỗn hợp thủy tinh thải và phụ gia thủy tinh lỏng sau khi nung ở cả nhiệt độ biến dạng và nhiệt độ nở phồng. Điều này mở ra tiềm năng ứng dụng của vật liệu xốp có nguồn gốc từ thủy tinh thải trong nhiều lĩnh vực khác nhau.
4. Kết luận
Trong nghiên cứu này, vật liệu xốp đã được tạo thành công từ thủy tinh thải và phụ gia thủy tinh lỏng ở các nhiệt độ nung 620oC và 830oC. Phân tích kính hiển vi nhiệt cho thấy 620oC là nhiệt độ bắt đầu biến dạng và 830oC là nhiệt độ nở phồng. Các kết quả phân tích khối lượng thể tích, độ xốp và độ hút nước cho thấy ở cả hai nhiệt độ nung đều tạo vật liệu xốp với độ xốp khá lớn. Trong đó, kết quả phân tích phân bố lỗ xốp cho mẫu nung ở 830oC có các tính chất xốp vượt trội hơn so với mẫu nung ở 620oC về cả kích thước lỗ xốp và khối lượng lỗ xốp. Nghiên cứu này chỉ ra rằng, tùy thuộc vào yêu cầu về kích thước và số lượng lỗ xốp của vật liệu, có thể lựa chọn nhiệt độ nung phù hợp để chế tạo vật liệu xốp từ thủy tinh thải.
LỜI CÁM ƠN:
Nghiên cứu này được tài trợ bởi Trường Đại học Quốc gia Thành phố Hồ Chí Minh (ĐHQG-HCM) trong khuôn khổ đề tài mã số C2024-20-22. Nhóm tác giả cũng xin cám ơn Trường Đại học Bách khoa, ĐHQG-HCM đã hỗ trợ thời gian, phương tiện và cơ sở vật chất cho nghiên cứu này.
TÀI LIỆU THAM KHẢO:
Rouquerol J, Avnir D, Fairbridge C W, et al (1994). Recommendations for the characterization of porous solids (Technical Report). Pure and Applied Chemistry, 66, 1739-1758.
Thach B K, Tan L N, Minh D Q, et al (2022). Production of porous glass-foam materials from photovoltaic panel waste. Green Materials and Electronic Packaging Interconnect Technology Symposium, 317-327.
Sooksaen P, Sudyod N, Thongtha N, et al (2019). Fabrication of lightweight foam glasses for thermal insulation applications. Materials Today: Proceedings, 17, 1823-1830.
Owoeye S S, Matthew G O, Ovienmhanda F O, et al (2020). Preparation and characterization of foam glass from waste container glasses and water glass for application in thermal insulations. Ceramics International, 46, 11770-11775.
Hesky D, Aneziris C G, Groß U, et al (2015). Water and water glass mixtures for foam glass production. Ceramics International, 41, 12604-12613.
Liao Y C, Huang C Y (2012). Glass foam from the mixture of reservoir sediment and Na2CO3. Ceramics International, 38, 4415-4420.
Bernardo E, Cedro R, Florean M, et al (2007). Reutilization and stabilization of wastes by the production of glass foams. Ceramics International, 33, 963-968.
Examining the foaming process in porous materials made from waste glass during the deformation and swelling stages
Do Quang Minh1
Huynh Ngoc Minh1
Kieu Do Trung Kien1
Nguyen Vu Uyen Nhi1
1Ho Chi Minh City University of Technology, Vietnam National University - Ho Chi Minh City
ABSTRACT:
Recycling glass into porous materials presents significant economic and environmental advantages. These materials exhibit high porosity, excellent thermal and sound insulation, fire resistance, and water resistance, making them valuable for diverse applications. This study investigates how the properties of porous materials derived from recycled glass evolve during two key thermal stages: the deformation stage (620°C) and the foaming stage (830°C). Experimental results confirm that sintering waste glass with water glass additives successfully produces porous materials. Notably, samples fired at the foaming temperature exhibit greater porosity than those processed at the deformation temperature, highlighting the impact of thermal treatment on material properties.
Keywords: glass recycling, recycling, pollution reduction, foam materials, waste glass powder.
[Tạp chí Công Thương - Các kết quả nghiên cứu khoa học và ứng dụng công nghệ, Số 3 tháng 1 năm 2025]